Interlocking sealing maintenance is a key component of the prevention and repair of common problems. According to statistics, one in three Americans has experienced or is experiencing a problem related to interlocking sealant issues. The purpose of this article is to provide insight into how preventive measures can be taken when it comes to these types of sealing maintenance issues.
The practice of interlocking sealing maintenance involves several steps that must be followed in order to ensure long-term protection and prevent potential damage caused by weathering, temperature changes, and other environmental conditions. In addition, proper installation techniques are essential for ensuring optimal performance over time. Furthermore, regular inspections should be conducted as part of any successful program for preventing common problems with interlocking sealing maintenance.
This article will discuss various methods for properly installing and maintaining an interlocking seal system so as to reduce the risk of future problems arising from improper use or inadequate protections against the elements. It will also explore some important considerations regarding inspection protocols and effective strategies for addressing any identified deficiencies before they become larger issues down the line.
Definition
Interlocking sealing maintenance is the practice of preserving and repairing a seal between two surfaces. It involves inspecting, cleaning, lubricating, or replacing seals to ensure that they remain intact and function correctly. The purpose of interlocking sealing maintenance is to prevent leaks, reduce wear and tear on equipment, and extend the life span of machinery.
Sealants used in interlocking sealing maintenance are typically composed of rubberized compounds, though other materials such as silicone may also be employed. These sealants must have good adhesion properties in order to effectively fill gaps between components and form an airtight barrier around any moving parts. Additionally, they must possess resistance against temperature changes and environmental factors so that their integrity remains intact over time.
The selection of an appropriate material for use in interlocking sealing maintenance will depend upon the application requirements and environment in which it will be exposed. As such, each situation should be considered individually when selecting a suitable sealant for any given application. With this knowledge, one can move forward into the next section about reasons for wear and tear.
Reasons For Wear And Tear
Maintaining interlocking sealings can be a difficult task, as the wear and tear of these components is inevitable. Understanding why certain parts become prone to damage over time is essential for proper maintenance. Euphemistically speaking, what may seem like gradual erosion in performance or appearance could actually be a sign of deeper issues that need attention. Here are some common reasons for such deterioration:
- Temperature fluctuations – Extreme temperatures can cause the material used in creating an interlocking sealing to expand or contract, leading to cracks and other damages.
- Exposure to chemicals – Chemical agents like solvents, acids and alkalis can corrode the surface of the seals which eventually leads to leakage.
- Poor installation methods – Improperly installed seals tend to loosen up more easily due to uneven pressure points along its circumference. This often results in leakage around the edges of the seal.
- Mechanical stress – Excessive vibration or shock caused by machines running nearby can lead to tears in the surface of the seal and reduce its effectiveness over time.
These factors have direct consequences on the life expectancy and functioning ability of interlocking sealing systems. Being aware of them helps ensure that any potential problems get addressed before they become too severe. As a result, it becomes much easier to keep all necessary equipment running smoothly with minimal disruption. The next section will cover proper cleaning techniques that help preserve and extend this type of system’s lifespan even further.
Proper Cleaning Techniques
When it comes to interlocking sealing maintenance, proper cleaning techniques are essential. It is important that the surface of the sealant be kept clean and free of dirt or debris before applying additional products. In order to do this, a soft cloth should be used along with warm soapy water and a mild detergent. After wiping down the surface, it should then be rinsed off with cold water for best results. Additionally, harsh chemicals such as acetone or paint strippers should not be used as they could damage the sealant material or cause discoloration.
Regular inspections can help identify any areas where regular cleaning may be needed. This includes checking around corners and edges for signs of buildup or discoloration which could indicate that more frequent cleaning is necessary in those areas. Inspections also provide an opportunity to spot potential problems early on before they become larger issues that require more extensive repairs down the road.
By following these simple steps, one can ensure their interlocking seals remain functional and long lasting for many years to come. The next step involves regularly scheduled inspections and repairs to help maintain the integrity of these components over time.
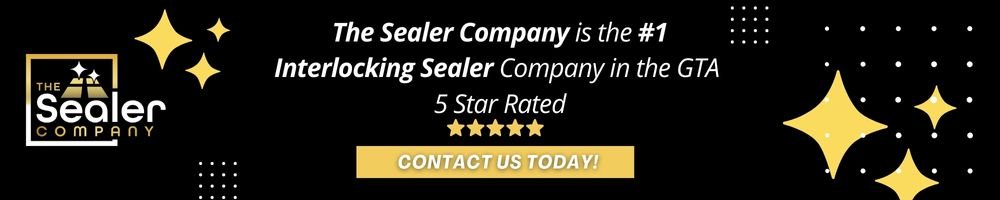
Inspections And Repairs
Once the proper cleaning techniques have been completed, it is important to inspect and repair any interlocking seals that may be exhibiting signs of wear or damage. This will ensure that these seals remain in good condition for as long as possible, preventing common problems from occurring. Regular inspections should be done at least every six months to identify potential points of failure. During an inspection, a visual check should be made to look for signs of cracking, chipping, warping or other physical damages on the seal surfaces. It is also important to perform a pressure test to make sure there are no leaks present in the system.
Any leaking seals should be immediately replaced by qualified personnel. If repairs need to be performed, they must follow all manufacturer instructions and safety guidelines. All equipment used during repairs must also meet applicable standards and regulations before being put into operation. The use of quality materials and tools when replacing parts will help extend their life expectancy and reduce costly breakdowns due to premature aging or corrosion. By following best practices for inspecting and repairing interlocking sealing systems, one can avoid many common problems with maintenance issues in the future.
Types Of Interlocking Seals
Interlocking seals are a vital component for the proper functioning of many machines and devices. There are several types of interlocking seals, each with their own advantages and disadvantages. The two main categories of interlocking seal designs include mechanical sealants and chemical sealants.
Mechanical sealants provide a physical barrier between components to prevent corrosion due to contact with liquids or other materials. They can be made from materials such as rubber, plastic, metal, or ceramic that form an accurate fit when installed correctly. Mechanical seals are well-suited for applications where tight tolerances must be maintained and require regular maintenance to ensure they remain in good condition.
Chemical sealants rely on chemical bonds to create an airtight area within a device or system. These sealants have excellent sealing capabilities but require special care during installation and servicing to avoid damaging the bond strength over time. Common chemicals used in this type of application include epoxy resins, silicone grease, Teflon paste, and RTV silicones. Chemical seals should be chosen carefully based on compatibility with the intended environment and selected material properties.
The right selection of interlocking sealant will depend greatly on the application requirements and environmental conditions expected during operation. Choosing the right sealant is critical for ensuring long-term performance and preventing common problems associated with improper maintenance or faulty installation techniques.
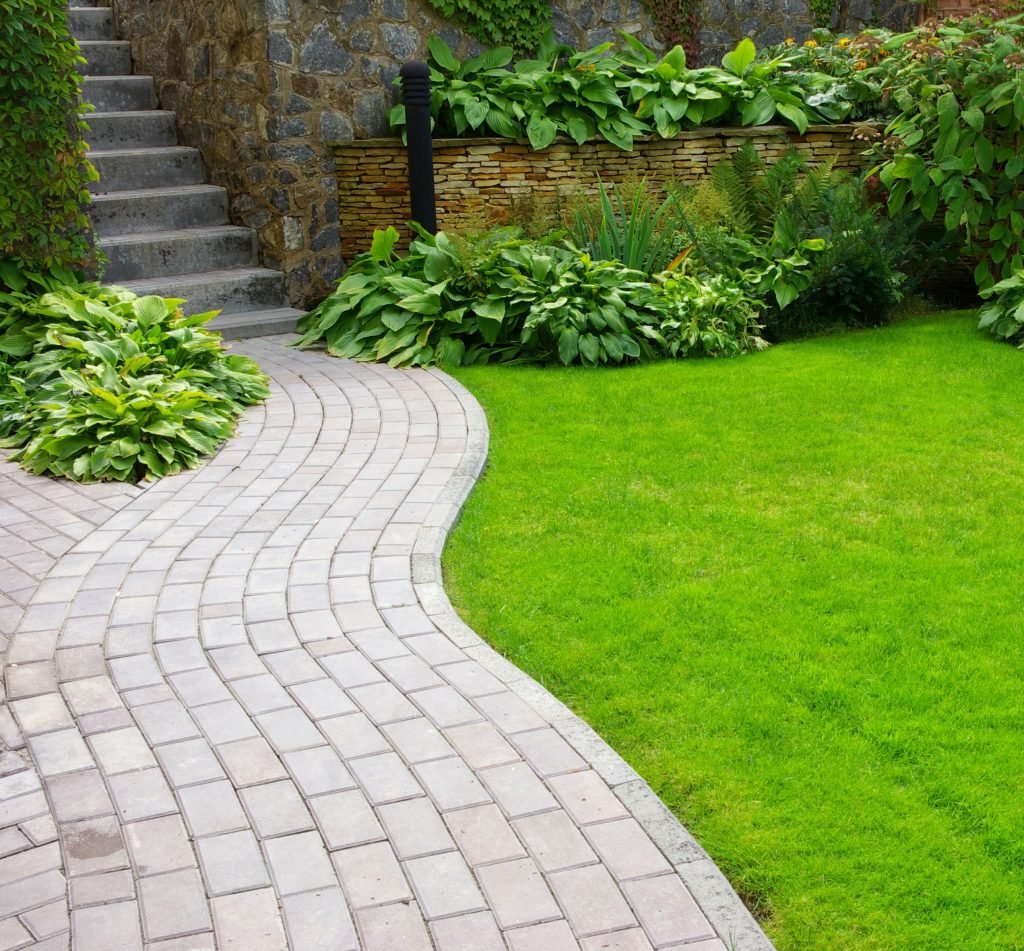
Choosing The Right Sealant
Choosing the right sealant is essential to ensuring a successful interlocking sealing maintenance program. With so many choices on the market, it can be tricky to select one that will provide adequate protection and longevity. Fortunately, there are some simple tips which can make selecting an appropriate sealant much easier.
First of all, you should always read labels carefully before making your purchase. This will help ensure that you choose a product with the properties and specifications necessary for your specific needs. For example, if you need a sealant for outdoor use, look for something specifically designed for this purpose so as to protect against rain or snow damage. Additionally, pay attention to any warnings about extreme temperatures or chemical exposure – such information could save time and money in the long run by avoiding costly repairs from improper installation or usage.
In addition to reading labels carefully, it’s also important to do research into different types of sealants available. Depending on what kind of materials you’re working with (such as wood or metal), certain products may be more suitable than others due to their compatibility and strength when exposed to environmental conditions over time. Similarly, some kinds of sealants may not be practical given the size of surfaces they need to cover; in these cases opting for smaller quantities might be more cost-effective while still providing sufficient protection.
As part of choosing the right sealant, consider consulting other professionals who have experience in this area – they may offer additional advice regarding product selection based on their own knowledge and expertise. Taking these steps ahead of time can prevent mistakes down the line that could lead to costly repairs or replacements later on. Transitioning into the subsequent section now, understanding how maintenance programs benefit interlocking seals is invaluable in helping extend their lifespan and ensure maximum performance over extended periods of time.
Benefits Of Maintenance Programs
Maintenance programs are essential in interlocking sealing systems to ensure their continued longevity and performance. Regular maintenance on these systems can identify potential problems before they become an issue, leading to fewer costly repairs down the road. Maintenance programs also provide a platform for early detection of issues that may arise due to age or other external factors, such as environmental conditions or mechanical wear. They also allow trained technicians to anticipate any changes that need to be made in order to avoid major breakdowns or malfunctions.
In addition, regular maintenance helps preserve the life span of the system by keeping components lubricated and free from dirt and debris build-up. This reduces the risk of unexpected damage caused by rust corrosion or friction between parts. Furthermore, it increases the efficiency of the system since all parts are kept functioning at optimal levels while minimizing energy consumption. Finally, preventive maintenance allows operators to better plan future needs based on current usage patterns, resulting in more cost effective operations over time.
The benefits provided by well-maintained interlocking sealing systems are numerous and should not be overlooked when planning for long term success. By proactively addressing potential issues through periodic inspections and routine servicing, businesses can help prevent common problems associated with these types of systems and enjoy greater financial savings in return. To further maximize the effectiveness of their investments, companies should strive to identify potential problems early to minimize downtime and maintain peak performance levels from their equipment.
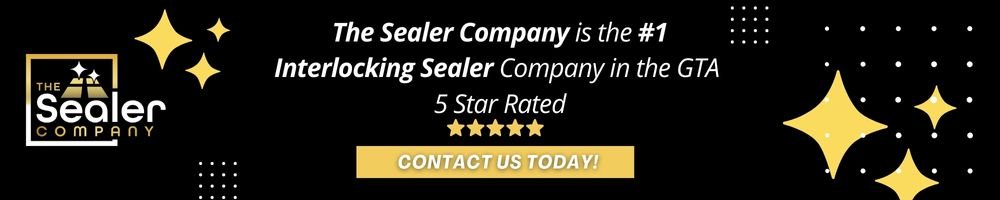
Identifying Potential Problems Early
In order to maximize the effectiveness of interlocking sealing maintenance programs, it is important to identify potential problems early. Early identification can allow for proactive preventative measures and limit any damage that may have occurred due to an issue being overlooked or ignored. This section will discuss three key indicators of potential issues with interlocking seals: wear and tear, contamination, and improper installation.
Wear and tear is a common cause of failure in interlocking seal systems. The quality of material used in construction as well as the frequency in which they are operated can both contribute to degradation over time. To mitigate this risk, regular inspections should be conducted on all parts involved in the system so that any signs of deterioration can be identified quickly. Additionally, it is beneficial to keep detailed records regarding how often each component has been used or replaced.
Contamination from various sources can significantly reduce the effectiveness of interlocking sealing systems. Dust, dirt, debris, chemicals, fluids, and other foreign materials must be kept away from these components at all times. Regular cleaning should be done using appropriate methods and products depending on what type of contaminants are present in the area where the seal system is located. It is also beneficial to install additional filters between high-pressure areas such as pumps and reservoirs where feasible.
Finally, improper installation of interlocking seals can lead to a number of potential issues down the line if not addressed immediately upon discovery. All components must fit properly according to manufacturer specifications in order for them to perform optimally without prematurely wearing out or causing other complications within the system itself. If there are discrepancies found during inspection then necessary adjustments should be made accordingly before putting them back into use again.
Adequate lubrication plays a vital role in ensuring optimal performance from interlocking seal systems throughout their lifespan; however, proper care must be taken when selecting lubricants since incompatible substances could corrode certain parts or otherwise negatively impact functioning capabilities.
Adequate Lubrication
Lubrication is the lifeblood of interlocking sealing mechanisms, allowing them to move freely with minimal friction. Like a car running on oil, this lubricant should be regularly checked and refilled as necessary. Many problems can arise from inadequate or incorrect lubrication: operating noises may increase, thermal expansion damage could occur due to increased temperature, and seal wear will accelerate. To ensure proper maintenance of an interlocking sealing system, it is essential that adequate lubrication be applied at all times.
The type and amount of lubricant used are also important considerations when maintaining interlock seals. While some parts require grease for effective operation, others may need light oils such as mineral or synthetic products instead. The specific requirements depend largely on the material composition of the components in question; thus they must be examined carefully prior to applying any sort of lubricant. It is also wise to check manufacturer specifications before using any product not approved by the equipment supplier.
By following these steps and ensuring sufficient quantity and quality of lubricating materials are applied where needed, many common issues with interlock seals can effectively be prevented. As part of regular inspection routines, personnel should inspect each component individually to verify its condition and if necessary apply additional lubricants accordingly. Smoothly transitioning into the next step towards reliable interlock performance requires correct alignment of parts – which we shall discuss further in our subsequent section.
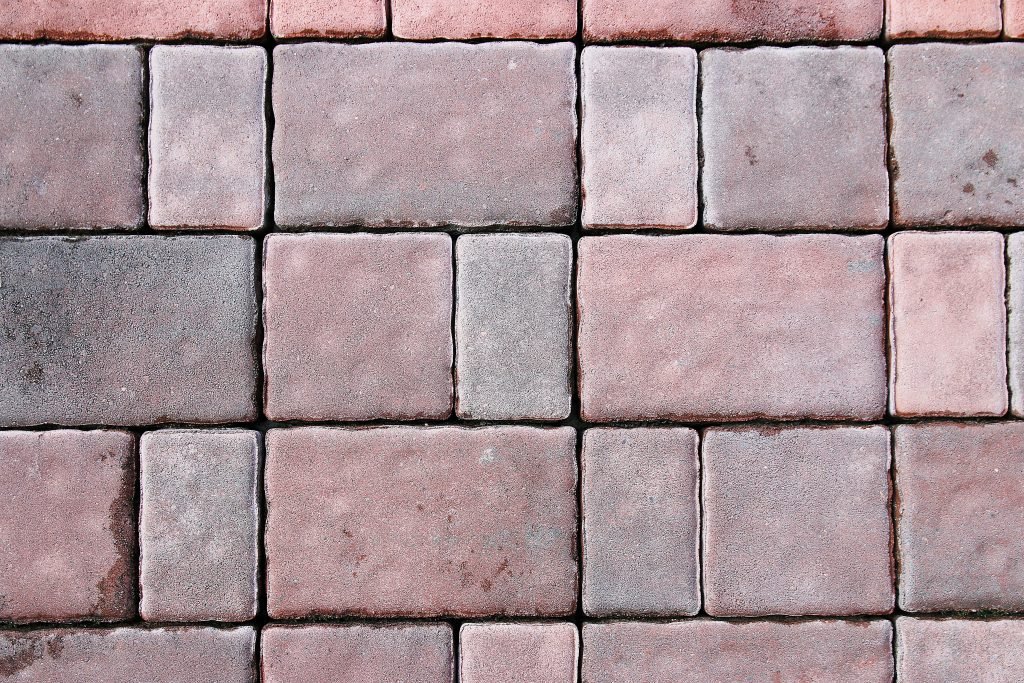
Correct Alignment Of Parts
Once proper lubrication has been achieved, the next step in preventing common problems with interlocking sealing maintenance is to ensure correct alignment of parts. If a seal fails due to misalignment between mating components, it can cause significant damage and costly repairs or replacement. To avoid this scenario, check that all seals are properly aligned before installation and adjust as necessary if they are not positioned correctly. Also inspect existing seals periodically for any signs of wear or strain caused by improper fitting.
The most effective way to prevent misalignment issues is to use hardened steel guide pins when installing new seals. Guide pins help keep two surfaces centered and maintain their relative positions during assembly operations. Additionally, consider using an adjustable jig fixture for precise placement of both end faces on the same plane before tightening the fasteners down on them. This will reduce binding forces and increase the life expectancy of your seals.
To further minimize potential misalignments from environmental changes such as vibration, temperature fluctuations, etc., monitoring environmental conditions should be considered an integral part of maintaining interlocking sealing systems.
Documentation Requirements
Having discussed the monitoring of environmental conditions, it is important to consider documentation requirements for interlocking sealing maintenance. Proper documentation ensures that data collected on environmental conditions can be accurately recorded and referred to when necessary. It also allows problems to be quickly identified and addressed in a timely manner.
The first step in documenting interlocking sealing maintenance is creating an appropriate system. This should include filing documents pertaining to any inspections or repairs carried out, as well as records of equipment used such as sealants and adhesives associated with the process. All relevant information must be kept updated, accurate, organized, easily accessible and securely stored. Additionally, regular reviews should take place to ensure all details are up-to-date and properly documented.
Finally, proper training should be given in regards to document handling procedures so that those who use them understand what is required from them in order to keep track of changes made over time. By ensuring these steps are taken care of not only will problems arising from improper interlocking sealing maintenance practices be avoided but also potential hazards caused by inaccurate recordings can be prevented. The next section will discuss contingency planning for emergencies related to interlocking sealing maintenance activities.
Contingency Planning For Emergencies
Interlocking sealing maintenance requires meticulous planning and implementation. The need to plan for contingencies is paramount. Planning in advance can prevent potentially disastrous consequences should an emergency arise due to inadequate preparation or lack of awareness.
It is essential that one develops a detailed strategy on how best to respond during any unforeseen circumstances, such as natural disasters, malfunctioning equipment, or other catastrophic events. All personnel involved must have comprehensive knowledge about the safety procedures and protocols that are necessary when dealing with these types of situations. Companies should also ensure that their staff is trained adequately and have access to appropriate resources so they can act quickly and efficiently if required.
Emergency plans should be regularly reviewed and updated to take into account changes in technology, regulations, and industry trends. This helps increase the effectiveness of responses while reducing mistakes from happening due to outdated information being used. Having reliable contingency plans in place gives peace of mind knowing there will be proper measures in place when needed most, enabling interlocking sealing maintenance operations to function smoothly even during difficult times. Professional training and education are key components here, ensuring all parties involved understand the importance of having robust solutions ready at all times.
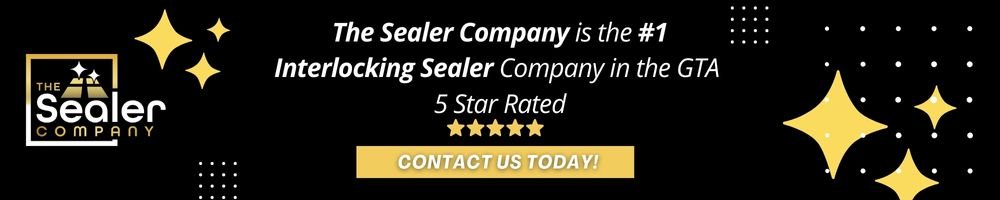
Professional Training And Education
Having an effective contingency plan in place is a crucial element for emergency preparedness. However, having properly trained personnel and educating them on the safety protocols associated with interlocking sealing maintenance can also help prevent common problems. Thus, it is essential to ensure that all facility staff receive regular training and education on this topic, as well as any other topics related to the equipment, machinery, and processes they are responsible for operating or supervising.
The first step is to provide formal instruction regarding the proper operation of such systems. During these sessions, technicians should be made aware of potential risks and hazards associated with their job responsibilities so they can take appropriate action in case something goes wrong. Additionally, supervisors should regularly review existing safety procedures and develop new ones if necessary. This will equip personnel with the knowledge needed to identify potentially hazardous situations before they arise and respond accordingly when one does occur.
In addition to providing formal instruction, facilities should also offer hands-on training where workers can practice using interlocking sealing maintenance techniques under direct supervision. Such practices will allow personnel to become more familiar with the system’s controls and gain confidence in their ability to operate it successfully without risking damage or injury due to improper usage. With proper training and education in place, facilities can rest assured that their employees are equipped with the skills required to safely operate interlocking seals while minimizing potential issues or accidents from occurring.
These measures will go a long way towards ensuring safe operations within each facility’s environment. As such, implementing professional training and educational programs is an important part of maintaining reliable interlocking sealing systems over time. By equipping staff with up-to-date information about all aspects of their jobs and reinforcing best practices through hands-on learning opportunities, organizations give themselves the best chance at avoiding costly incidents stemming from unsafe handling of equipment or processes related to interlock sealing maintenance . Ultimately, prioritizing safety protocols ultimately helps create a safer working environment for everyone involved.
Safety Protocols
The safety of personnel is of utmost importance when it comes to interlocking sealing maintenance. Adherence to all relevant safety regulations, including the use of personal protective equipment (PPE), should be strictly enforced. Appropriate PPE items include gloves and other types of clothing that provide adequate protection from heat, sharp edges, dust, chemicals and any hazardous materials being handled during work operations. All employees must also be trained in emergency procedures for dealing with potential hazards or accidents that may occur while working on a machine.
In addition to wearing appropriate PPE, proper handling techniques should always be used when performing maintenance tasks such as removing cover plates and inspecting components inside the machine. The installation or removal of parts should never be performed without first disconnecting the power source to avoid electric shock or injury. It is also important to ensure that all tools are properly stored after each use so they do not pose a hazard when not in use.
Regularly scheduled inspections can help detect problems early before they become too serious and lead to costly repairs or downtime. Inspections should include visual checks for loose bolts and damaged seals, checking operating temperature levels within acceptable ranges and ensuring lubrication points are free from contamination. This helps extend the life of an interlock seal system and ensures safe operation at all times.
Conclusion
The proper maintenance and care of interlocking seals is essential in order to avoid major problems. With careful consideration and meticulous inspections, the risk of faults can be minimized while prolonging the life of any machinery with interlocking seals. Regular check-ups are key to detecting wear and tear or other potential issues before they become serious.
It is important that the right sealant is chosen for each application based on its intended use, as well as the correct lubrication applied regularly for optimal performance. A thorough understanding of safety protocols must also be followed when working with these types of seals to ensure a safe environment for all personnel involved.
In conclusion, keeping an eye out for signs of damage or deterioration and adhering to both preventive measures and repair instructions will go far in preventing common problems associated with interlocking sealing maintenance. Through conscientiousness combined with knowledgeability, it is possible to protect your equipment from costly breakdowns so that you may continue enjoy reliable service without interruption.
Frequently Asked Questions
How Often Should Inspections And Repairs Be Carried Out?
Regular inspections and repairs of interlocking sealing maintenance are essential for preventing common problems. The frequency of these checks should be determined based on the size and complexity of the system, as well as any other factors that may affect its performance. Generally speaking, however, it is recommended to inspect the system at least once per year. In some cases, more frequent evaluations may be necessary depending upon environmental conditions or recent changes in equipment configuration.
During an inspection, a qualified technician will assess the condition of all components in order to identify potential issues before they become serious problems. This includes checking seals and connections for signs of wear or damage as well as verifying proper operation and functionality of any automated systems such as sensors or valves. Any irregularities found during this process can then be addressed with either repair or replacement parts. Additionally, it is important to ensure that lubrication levels are adequate to keep moving elements working properly over time.
In addition to regular inspections, periodic maintenance activities must also be carried out in order to maintain peak efficiency from your interlocking sealing systems. These tasks may include cleaning dust and debris from interior components; replacing seals when needed; performing lubrication treatments; inspecting electrical wiring for corrosion; testing pressure relief valves; etc. Allowing professionals to take care of these procedures will help extend the life expectancy of your equipment while ensuring safe operation and maximum reliability over time.
What Should I Consider When Choosing The Right Sealant?
When choosing the right sealant, there are several factors to consider. Firstly, the surface of application must be taken into account; some surfaces may require different types of sealants than others. Additionally, it is important to determine what environmental elements will affect the performance of the sealant and select one that can withstand these conditions. Furthermore, any potential chemical reactions between the sealant and other compounds should also be considered before making a purchase. Here is a list of key points to remember:
- Check for compatibility with existing materials
- Consider what environment the sealant will face daily
- Research any possible chemical reactions from use
- Select an appropriate product for specific applications It is critical to research thoroughly and pick a suitable product for each specific situation in order to ensure successful sealing maintenance over time. Careful consideration when selecting a sealant will help prevent problems down the line and ultimately save resources.
How Can I Identify Potential Problems Early?
Identifying potential problems early on is a key part of maintaining interlocking sealing systems. Taking the right action at the right time can make all the difference in preventing costly, extensive damage. To truly understand how to identify these issues before they become too severe, it’s important to have an understanding of what makes a quality sealant and how its components interact with each other over time.
When selecting a sealant, factors such as durability, adhesion properties, ability to resist heat/cold/weathering, curing process and ease of application should be taken into account. Sealants are made from different materials – polyurethane foam or silicone for example – so researching their benefits and drawbacks is essential when making a choice. Additionally, any health concerns related to toxic fumes should also be considered. It’s wise to choose one that has been tested thoroughly by experts in your field.
The best way to prevent major issues down the line is through regular inspection and maintenance; this includes checking seals for cracking or splitting due to temperature changes or long-term wear and tear. If any evidence of deterioration is found then steps must be taken swiftly to replace the affected area with fresh sealant. Leaks should not be ignored as they could potentially cause serious structural damage if left unattended for prolonged periods of time. In order to detect even slight signs of degradation it’s advisable to use tools such as moisture detectors which can quickly diagnose problem areas without damaging existing surfaces.
Properly assessing sealants prior to installation and carrying out routine inspections thereafter will go some way towards ensuring successful outcomes for interlocking sealing maintenance projects – avoiding costly repairs and downtime in the future whilst guaranteeing reliable performance every step of the way.
What Type Of Lubrication Is Best For Interlocking Seals?
When it comes to interlocking seals, the type of lubrication used is important. Selecting the right lubricant helps ensure a reliable seal and can help prevent common problems from occurring. To identify which lubricants are best suited for interlocking seals, consider the following:
-The amount of force or torque needed to turn multiple parts together
-The temperature range in which the mechanism must operate
-The environment in which the components will be operating
-Expected life cycle of the components
To choose an appropriate lubricant, many factors should be taken into consideration such as viscosity, base oil characteristics and additives contained within the formula. Viscosity refers to how thick or thin a liquid is; thicker liquids do not flow as easily while thinner ones flow more freely.
Base oils provide a medium through which other ingredients, like friction modifiers and antiwear agents, are suspended. These materials work together to improve performance and extend component life by reducing wear on working surfaces that come into contact with one another during operation. Finally, some lubricants contain additional additives designed to further enhance their performance capabilities in specific environments and applications.
In summary, when selecting an appropriate lubricant for use with interlocking seals there are several factors that need to be considered including viscosity, base oil characteristics, additives present in the formula, required force/torque levels, temperature ranges and environmental conditions where components will be operating. Additionally, expected lifecycles should also be taken into account when making this decision so that optimal performance can be achieved over time.
What Are The Safety Protocols For Working With Interlocking Seals?
Like a set of dominoes, interlocking seals are delicate pieces that must be handled with care. Malfunctioning or misaligned sealing can cause widespread consequences for industrial and commercial machinery. Therefore, understanding the safety protocols related to working with these types of seals is essential for avoiding common problems in maintenance.
When dealing with interlocking seals, it is important to take into account the material used in their construction as this will determine what type of lubricant should be applied during service intervals. Generally speaking, sealants made from silicone rubber require synthetic oils such as polyalphaolefins (PAO) while PTFE-based materials need special greases containing molybdenum disulphide or graphite. In any case, using excessive amounts of lubrication should be avoided.
Finally, personnel handling interlocking seals must wear appropriate protective gear like gloves, goggles and face masks when servicing them due to the presence of small particles which may become airborne if disturbed by careless movements –– potentially leading to health issues. Furthermore, ensuring all components are correctly assembled prior to use is key for preventing serious malfunctions down the line. Keeping these safety protocols in mind can help minimise risks associated with operating and maintaining interlocking seals.